Essential Devices and Tools for Effective Metal Stamping Workflow
Essential Devices and Tools for Effective Metal Stamping Workflow
Blog Article
Taking Full Advantage Of Efficiency and Quality With Cutting-Edge Steel Stamping Techniques
In the realm of steel stamping, the search of operational quality through the assimilation of ingenious approaches is vital. As industries progress and demands for precision and performance boost, remaining ahead of the contour becomes a critical essential. By welcoming sophisticated technologies and procedure enhancements, organizations can open brand-new levels of efficiency and item quality. The crossway of sophisticated steel stamping methods, automated systems, rigorous high quality controls, and lean production concepts offers a tantalizing look right into the future of manufacturing. This convergence holds the assurance of not just meeting yet exceeding market criteria, establishing the stage for unrivaled performance and consumer fulfillment.
Advanced Steel Stamping Technologies
In the world of steel stamping, the combination of cutting-edge modern technologies has actually changed the sector, boosting accuracy and performance in making procedures - Metal Stamping. Advanced steel stamping innovations have played a critical role in elevating the capabilities of producers, enabling for more elaborate designs and higher production rates
Among one of the most considerable improvements in metal stamping modern technology is the execution of computer system numerical control (CNC) systems. CNC systems enable precise control over the stamping process, causing precise and consistent manufacturing of facility parts. Additionally, using servo presses has actually produced enhancements in energy performance and lowered cycle times, better optimizing the manufacturing procedure.
In addition, the assimilation of automation and robotics has structured steel marking operations by enhancing efficiency and decreasing the threat of mistakes. Automated systems can carry out jobs with rate and accuracy, leading to boosted overall performance in the assembly line.
Automated Procedures for Efficiency
Use of automated processes in steel stamping procedures has actually substantially enhanced effectiveness and performance in producing centers (Metal Stamping). Automated systems have reinvented the steel stamping market by streamlining processes, lowering manual treatment, and minimizing the margin of mistake. These automated solutions include a variety of technologies, consisting of robotic arms, CNC devices, and computerized control systems, that job cohesively to perform detailed stamping jobs with precision and rate
One primary benefit of automated processes in steel stamping is the regular quality they supply. By getting rid of human mistake and variations in manufacturing, automated systems ensure that each stamped component satisfies specific specs with very little flaws. Automation allows constant procedure, significantly decreasing downtime for tool modifications and upkeep, therefore taking full advantage of total performance.
Additionally, automated processes improve security in steel marking procedures by lessening the demand for manual handling of heavy materials and sharp devices. This not just safeguards employees however likewise adds to an extra structured and effective workflow. In conclusion, the integration of automated processes in steel marking procedures is essential for accomplishing Home Page ideal effectiveness, top quality, and safety and security standards in modern manufacturing environments.
Quality Control Steps in Marking
Offered the focus on constant high quality and performance attained via automated processes in metal marking procedures, implementing robust quality control measures becomes vital to maintain requirements and guarantee accuracy in stamped parts. Quality control in metal stamping entails a multi-faceted strategy to assure the integrity and accuracy of the final products. By integrating these steps into metal marking procedures, suppliers can regularly create top notch stamped parts that fulfill the stringent demands of modern sectors.
Enhancing Precision Through Technology
To accomplish unequaled precision in steel stamping processes, introducing developments are continuously being created and integrated right into the manufacturing workflow. Advanced modern technologies such as laser cutting systems and computer system numerical control (CNC) machines have actually transformed the means metal components are marked with utmost accuracy. By making use of laser cutting modern technology, makers can achieve detailed and complicated styles with micron-level accuracy, making sure that each stamped part fulfills the strictest top quality requirements.
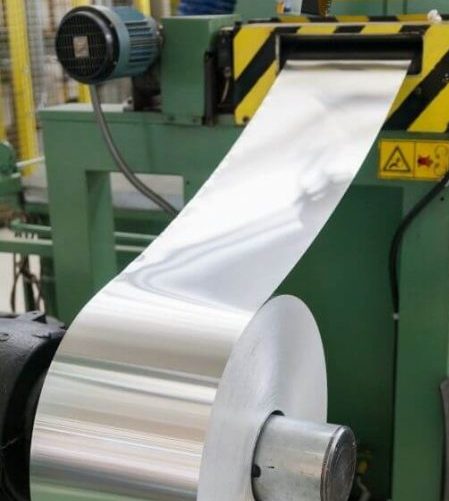
Moreover, using simulation software application enables makers to examine and enhance stamping processes before real manufacturing, recognizing prospective areas for improvement and fine-tuning parameters to attain optimum accuracy. By embracing these innovative technologies, manufacturers can boost accuracy, boost efficiency, and deliver high-quality stamped items that fulfill the most stringent needs of modern-day markets.
Executing Lean Production Practices
Integrating lean production methods right into metal marking procedures can lead to streamlined manufacturing procedures and increased general efficiency. By focusing on removing waste, optimizing resources, and continually enhancing procedures, metal marking companies can improve performance and quality while minimizing prices.
Furthermore, lean production practices motivate a culture of continual improvement within the organization. By equipping staff members to identify and attend to inadequacies, companies can make incremental changes that cause substantial performance gains over time. Implementing devices such as 5S, Kanban systems, and value stream mapping can assist enhance procedures, lower preparations, and boost total quality in metal stamping processes.
Conclusion
To conclude, the usage of sophisticated steel stamping innovations, automated processes, quality assurance procedures, advancement for precision enhancement, and application of lean manufacturing methods are vital for making the most of efficiency and see here quality in steel marking procedures. These methods make sure that products are produced with precision, uniformity, and cost-effectiveness. By incorporating these sophisticated strategies, makers can stay affordable in the sector and satisfy the demands of consumers successfully.
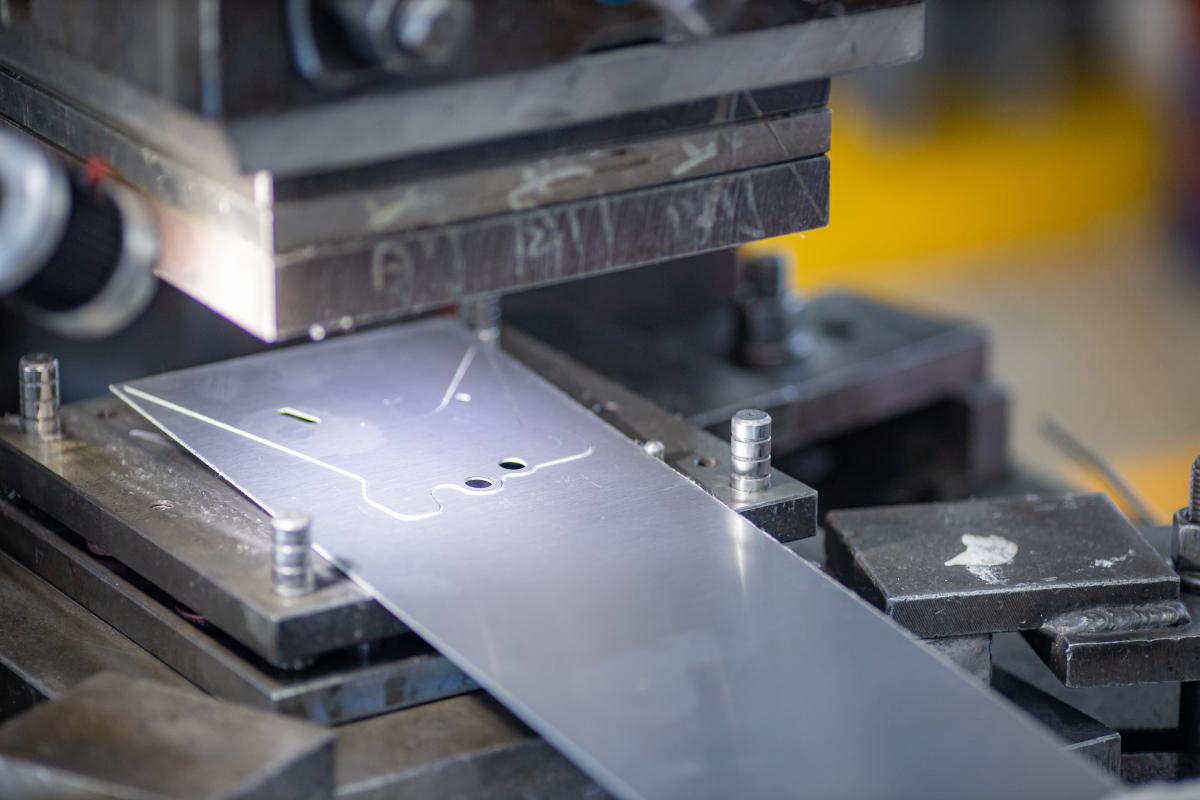
Provided the focus on regular top quality and performance attained through automated processes in metal stamping operations, executing robust high quality control procedures comes to be important to maintain criteria and make certain precision in stamped parts. Executing tools such as 5S, Kanban systems, and value stream mapping can help improve operations, decrease lead times, and boost total quality in metal stamping procedures.
In verdict, the application of innovative steel stamping technologies, automated processes, quality control measures, innovation for precision enhancement, and application of lean production techniques are crucial for optimizing effectiveness and high quality in metal marking procedures.
Report this page